Stroke End Block-DGEB
The Stroke End Block DGEB is a high-performance component designed to maintain accurate positioning within press-in die systems. Engineered to withstand high-stress environments, the DGEB block ensures stable and precise alignment of die components during press operations. Its durable construction reduces wear, prolongs die life, and minimizes maintenance needs. Ideal for industrial applications, the Stroke End Block DGEB supports consistent, efficient press performance by preventing misalignment and enhancing the overall operation.
The Stroke End Block DGEB is a high-precision component designed to provide reliable positioning and alignment in press-in die systems. It plays a crucial role in ensuring that die components remain accurately aligned during press operations, maintaining the proper stroke and preventing misalignment or shifting. This component is especially important in high-stress industrial environments, where consistent, stable performance is necessary to avoid costly production errors and reduce downtime.
Crafted from durable, wear-resistant materials, the DGEB Stroke End Block is engineered to withstand the repetitive forces and heavy loads associated with press operations. Its robust design not only helps to maintain the correct position of die components but also reduces the risk of wear and tear, which can extend the lifespan of the die system and lower maintenance costs.
By incorporating the Stroke End Block DGEB into press-in die setups, manufacturers can ensure more efficient press cycles, as the block keeps the die in the correct position throughout each operation. This consistent positioning prevents misalignment and reduces the likelihood of production defects, ensuring high-quality output and reliable performance across multiple press cycles.
The DGEB Stroke End Block is an essential tool for manufacturers looking to enhance press efficiency, reduce maintenance, and maintain die longevity. Its ability to withstand challenging industrial conditions while maintaining precise die alignment makes it a valuable component for improving operational productivity, reducing wear on press equipment, and optimizing overall press-in die performance.
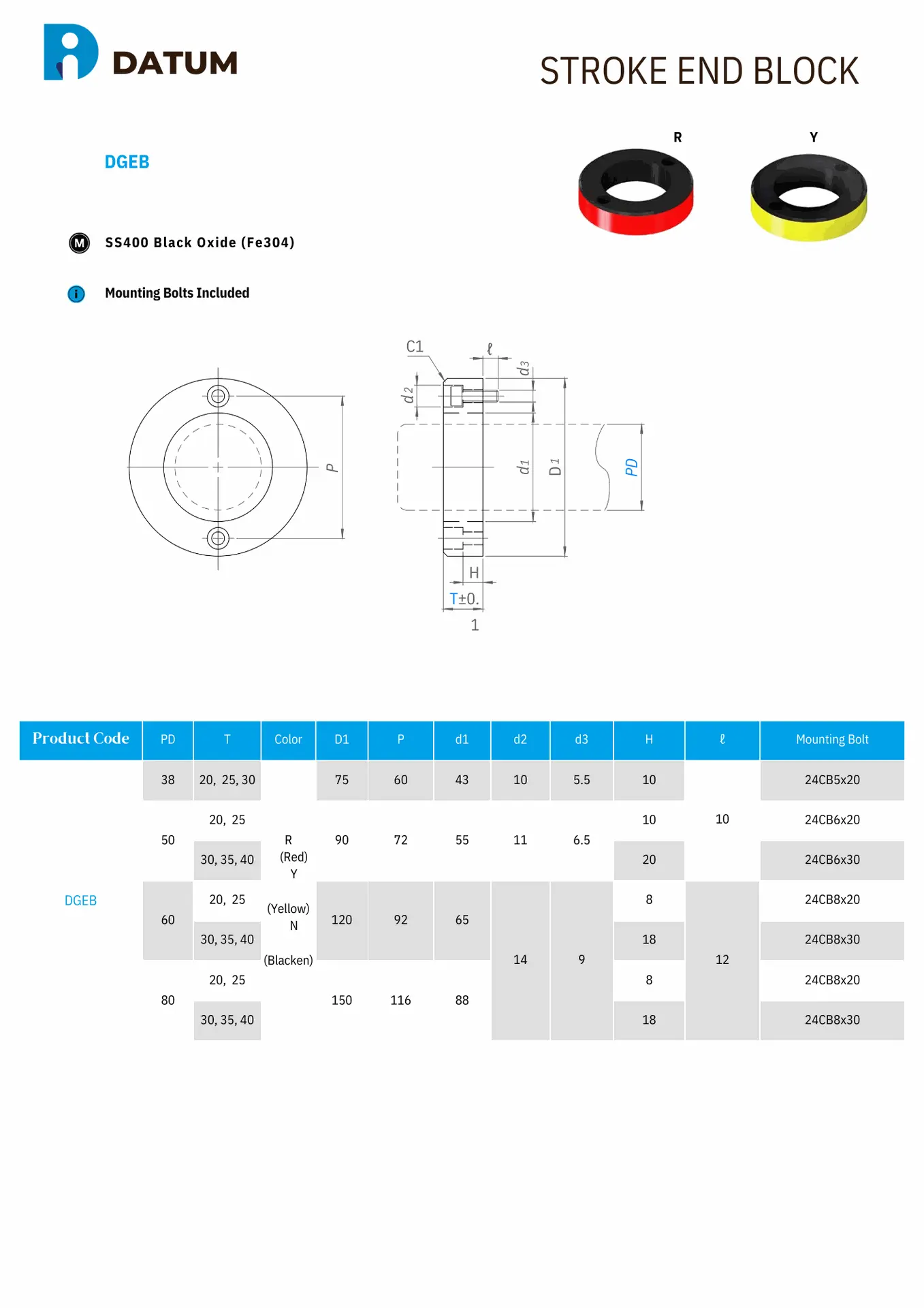