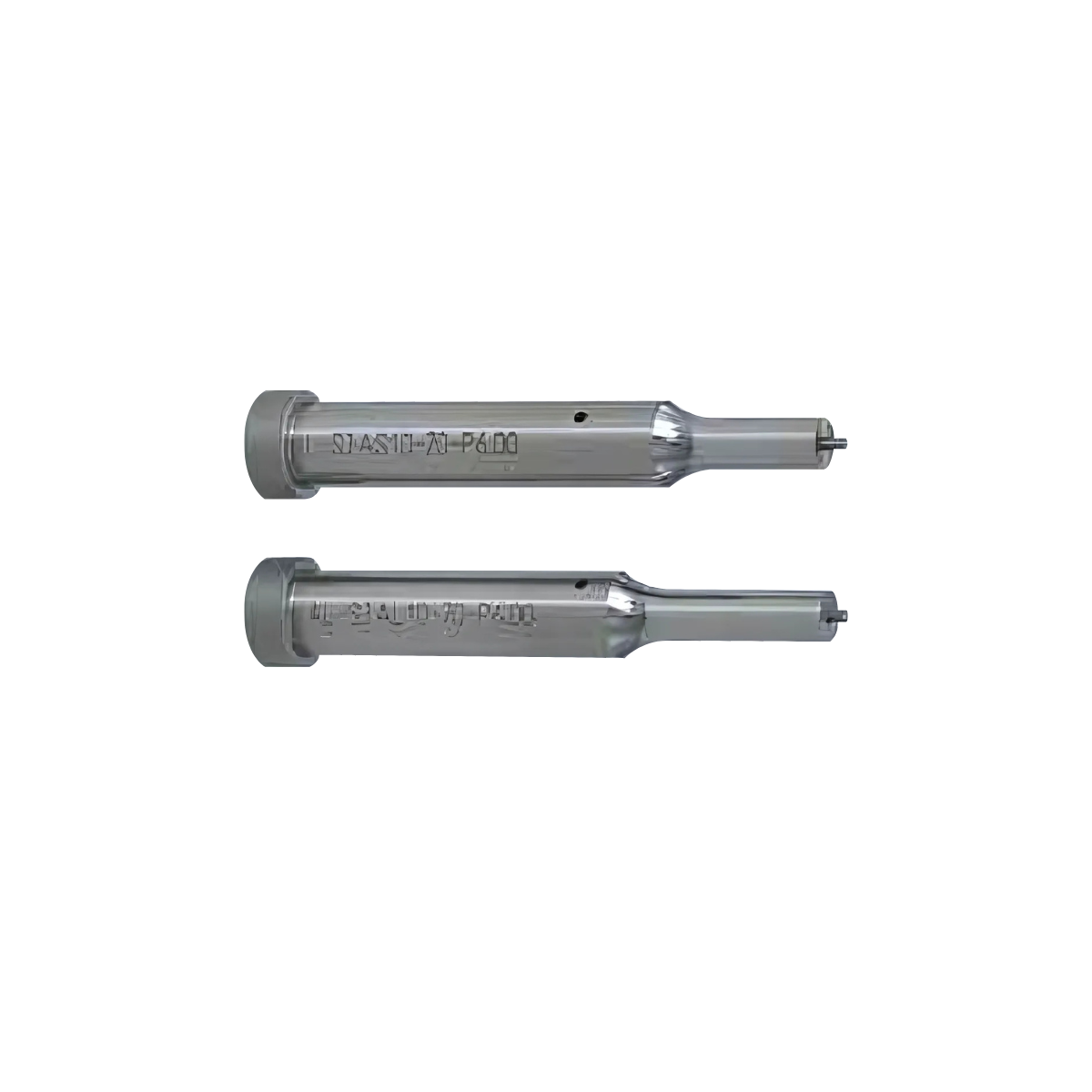
JECTOR PUNCHES
Lapping
Jector Punches with Lapping are specially designed for high-precision applications in press-in-die operations. The lapping process enhances the surface finish, ensuring smooth and accurate performance. These punches maintain their position with exceptional stability under heavy load conditions, resulting in consistent, reliable results. Ideal for industries requiring precise and efficient tooling, Jector Punches with Lapping offer extended tool life, reducing the need for frequent replacements. Enhance your manufacturing process with Jector Punches, engineered for superior wear resistance and durability in high-demand press-in-die applications.
Jector Punches with Lapping are a vital component for achieving optimal performance in maintain position press-in-die applications. These punches are precisely designed and undergo a meticulous lapping process, which refines their surface finish for superior precision and smooth operation. The lapping process enhances the punch's durability, making it ideal for high-load conditions and ensuring minimal wear over time. This results in reliable, accurate punching while maintaining the required position in the die, which is crucial for efficient production cycles.
Perfect for industries that demand high precision and durability, Jector Punches with Lapping reduce the frequency of tool replacement, offering both cost and time savings. The enhanced surface finish helps prevent friction, providing smoother functionality and a longer lifespan for the tooling.
Whether you're working with heavy-duty applications or intricate designs, these punches deliver exceptional performance under pressure, even in challenging production environments. With a focus on longevity and efficiency, Jector Punches with Lapping offer a high level of operational consistency, helping businesses achieve their production goals effectively.
Optimize your manufacturing process with Jector Punches with Lapping and experience a reliable, long-lasting tool that ensures precision, reduces maintenance costs, and boosts overall productivity in press-in-die operations.
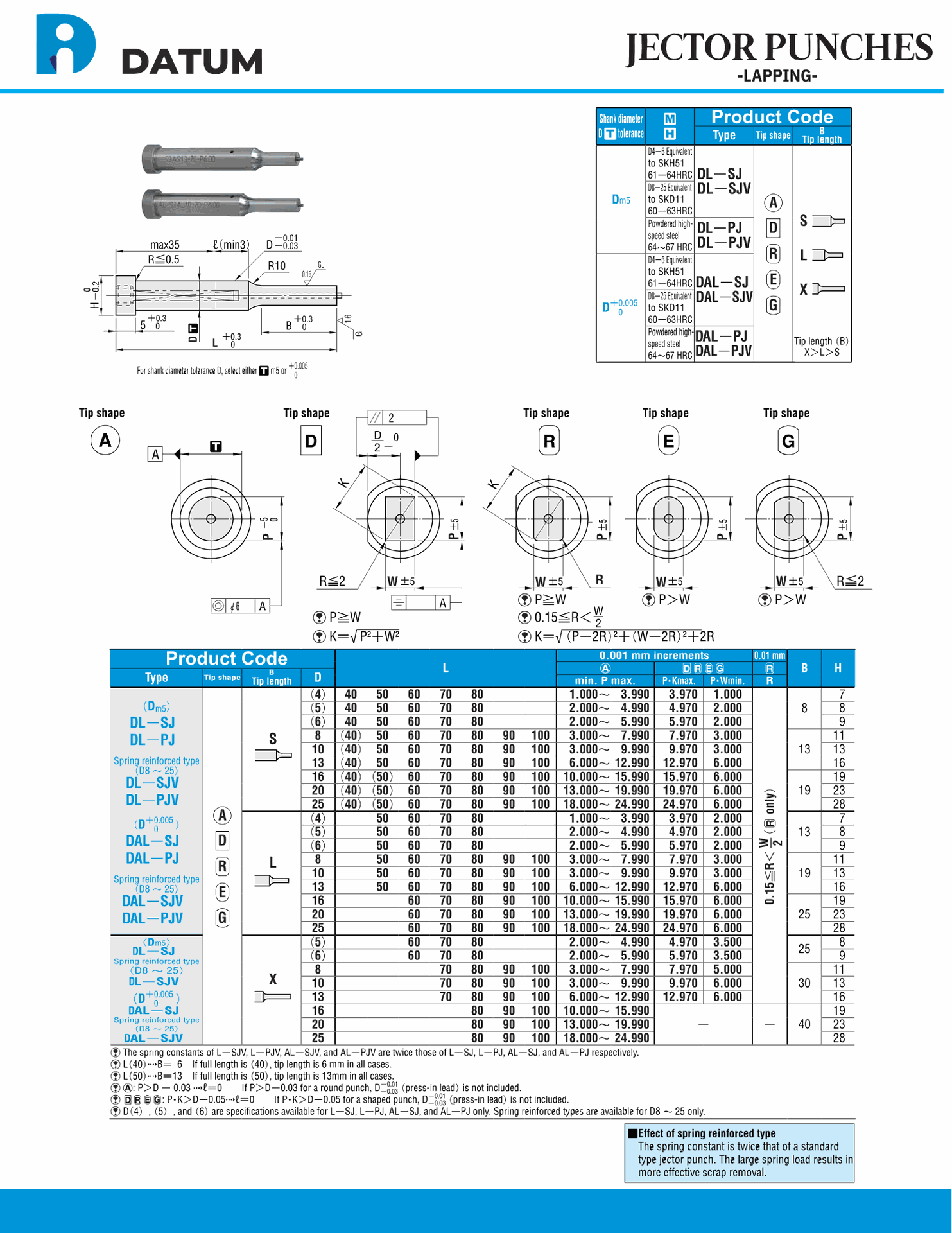
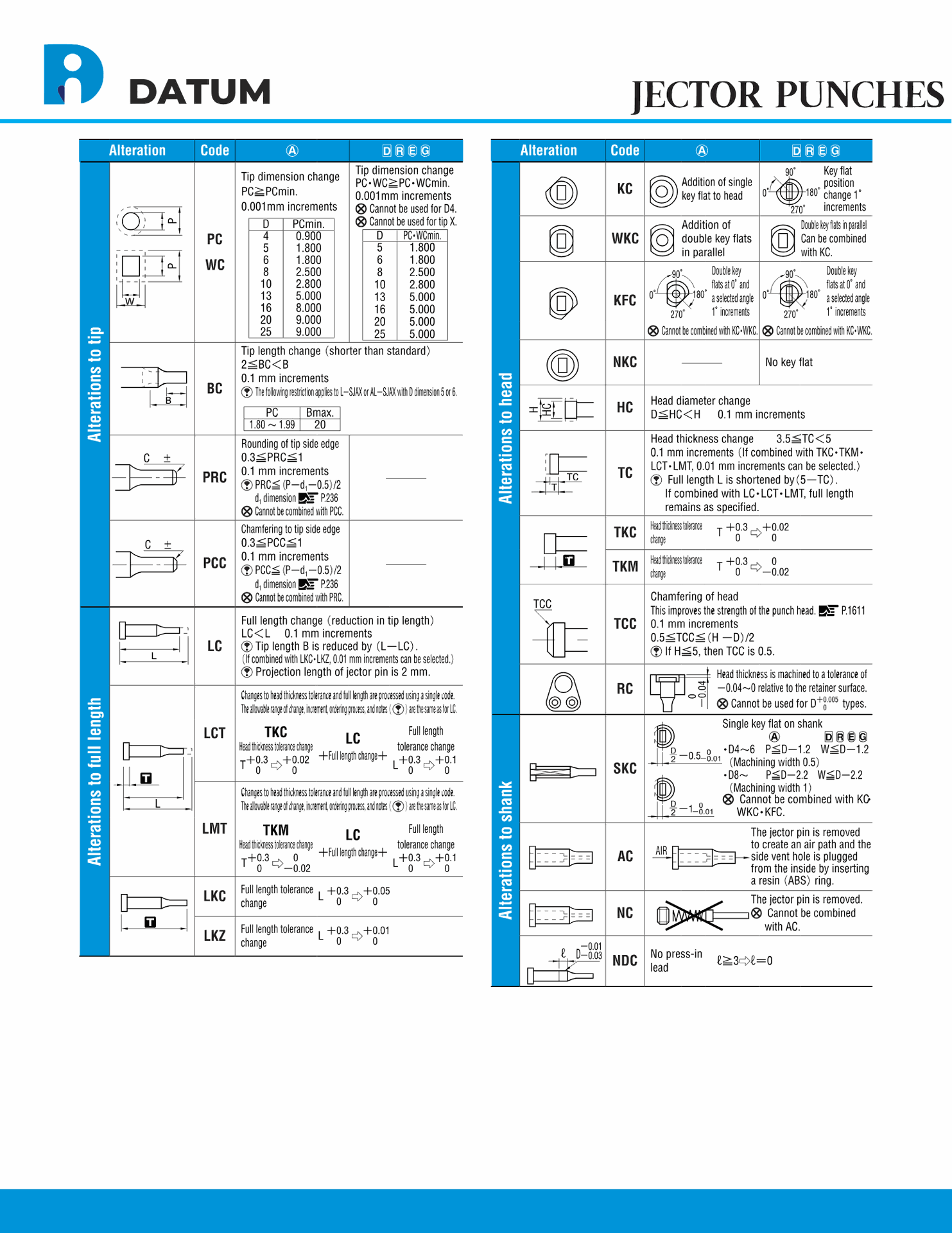