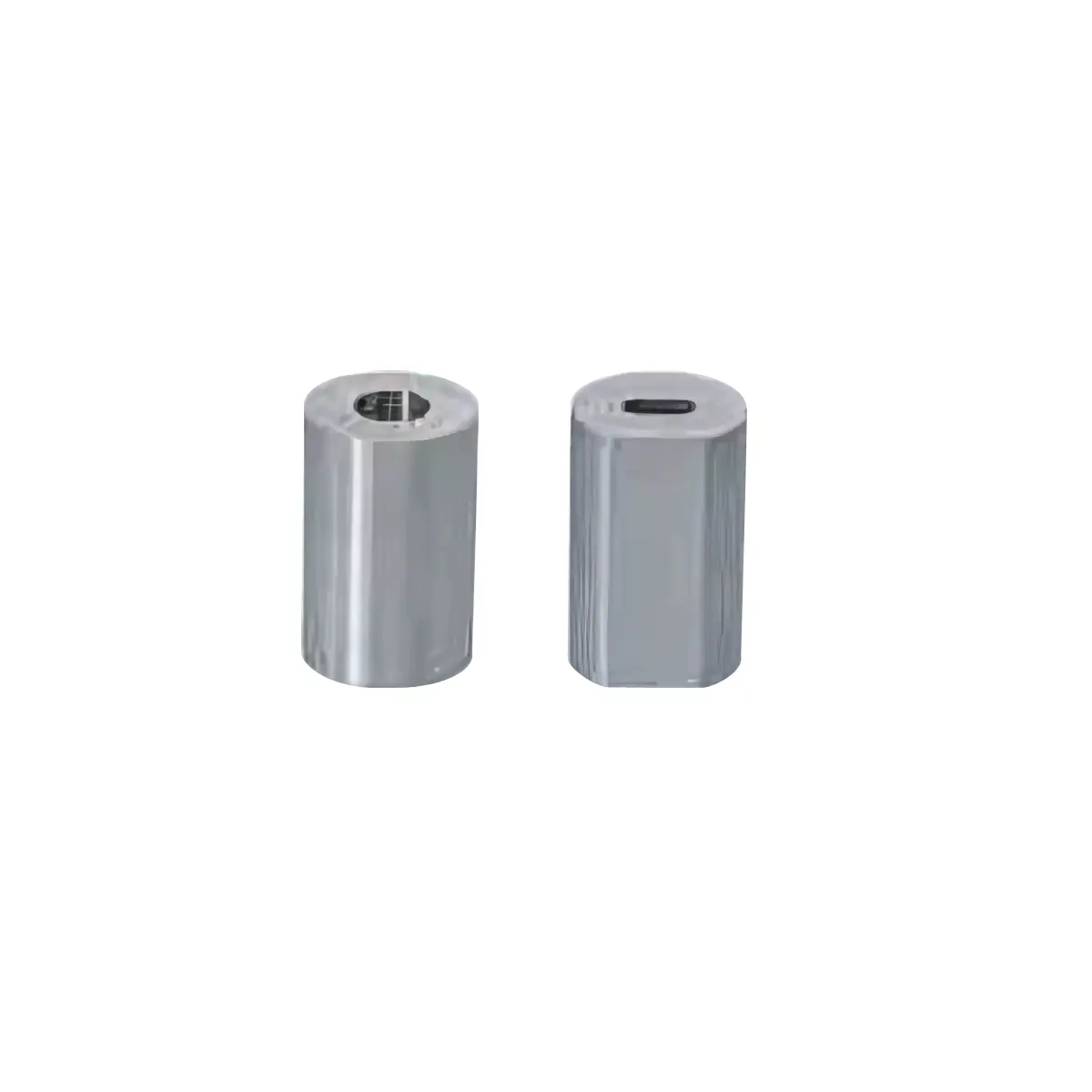
SCRAP RETENTION
Reverse Angular Buttons Dies (straight Type)
Reverse angular buttons dies (straight type) are precision-engineered components for effective scrap retention in maintain position press dies. The straight design, combined with a reverse angular profile, ensures secure scrap holding, preventing interference and maintaining a clean stamping process. Designed for durability, these dies perform reliably under high-speed and high-pressure conditions. Ideal for industries like automotive and electronics, they enhance production efficiency, reduce downtime, and ensure consistent, high-quality results. Optimize your stamping operations with reliable scrap retention solutions tailored for modern manufacturing needs.
Reverse angular buttons dies (straight type) are essential components designed to ensure effective scrap retention in maintain position press dies. These dies feature a straight design paired with a reverse angular profile, enabling them to securely hold scrap material during the stamping process. By preventing loose scrap from interfering with operations, they maintain a clean and efficient workspace, which is critical for achieving high-quality stamping results.
The straight type construction provides a balance of simplicity and precision, making these dies ideal for high-speed and high-pressure applications. Their robust design ensures durability and long-lasting performance, reducing the need for frequent replacements and minimizing downtime.
Reverse angular buttons dies (straight type) are particularly suited for industries like automotive, aerospace, and electronics manufacturing, where precision and operational efficiency are paramount. These dies contribute to improved production consistency by minimizing scrap-related disruptions and protecting other press components from potential damage caused by stray material.
Investing in reverse angular buttons dies (straight type) enhances the reliability of stamping operations, ensuring consistent performance and high-quality outputs. They offer a cost-effective solution for manufacturers seeking to streamline their processes, reduce waste, and optimize overall productivity in metal stamping applications.

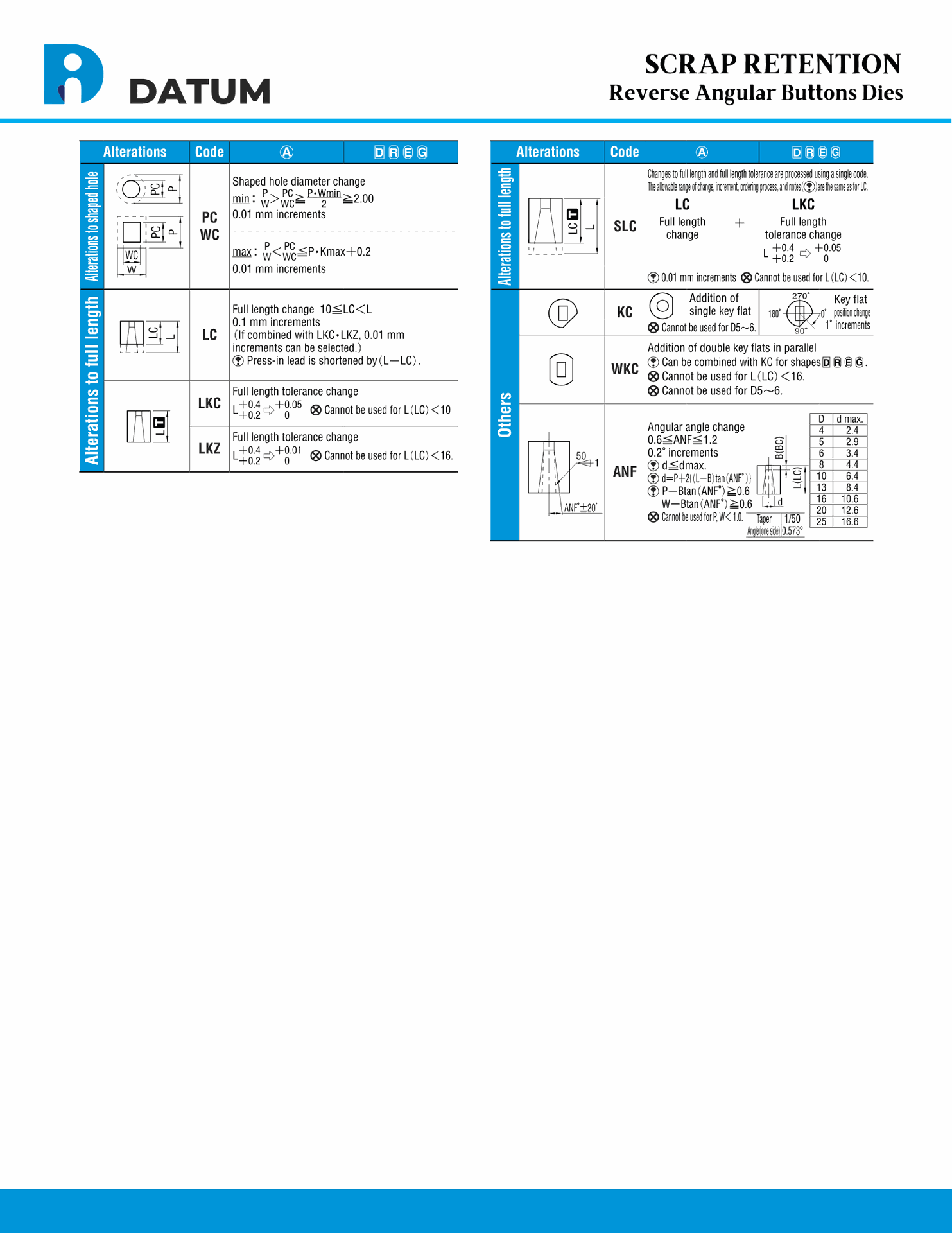